- June 24, 2024
- Posted by: Tom Richert
- Categories: Leadership, Performance Leadership
By Brenden Lydon, John DaSilva, and Tom Richert
Introduction
In late May of 2023 Wise Construction began the renovation of a 20,000-square-foot hospital wing that provides Newton-Wellesley Hospital outside of Boston with a 24-bed medical/surgical unit. The planned schedule accommodated substantial completion of the work by April 5, 2024, so the hospital could prepare the space to be available for patients on May 20. This schedule was established with the understanding that permit documents would be available by the end of June to allow for an August 14 issuance of a building permit. Before the permit was to be issued Wise was able to begin enabling work that included demolition and the cut-over of some utilities.
Unanticipated issues not related to actual construction resulted in a delay of the issuance of the building permit until October 12, placing the project nine weeks behind schedule. With the community need for these patient rooms the hospital requested that Wise find a way to achieve substantial completion by the original April 5 date.
Four core actions taken contributed to Wise meeting this challenge.
- Employing a strategic pull planning approach for systems rough-in phase planning that focused on creating clearly illustrated workflows, allowing for plan modifications to meet target inspection dates.
- Using this strategic approach for collaboratively planning interior finishes workflow that allocated small zones to trade operations, allowing later trades to begin and complete work sooner than is the case with conventionally planned projects.
- Daily management of weekly plan commitments from trades that aligned with the pace established in the systems rough-in, interior finishes, and commissioning phase planning sessions.
- Twice weekly onsite reviews with project designers that promoted rapid problem solving to prevent delays that can impact fast-moving projects being built in an existing space.
Implementing Lean Construction Practices
Prior to learning about the permit related delay Wise committed to implementing lean construction practices on the project, including use of the Last Planner System® to coordinate the activities of trades working in the space. Initial implementation planning began in late June, with the initial planning of systems rough-in work performed on July 11. This planning used a pull planning approach consistent with Last Planner System phase planning practices. Representatives from the hospital, Colliers Project Leaders, the project owner’s representative, Keel Project Management, the owner’s project advisor, Perkins&Will, the project architect, and BR+A Consulting Engineers, the project MEP engineer, participated with trade contractors in the planning session.
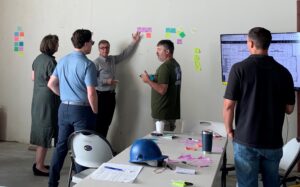
The systems rough-in phase plan mapped workflows through four zones on the floor, with most trades working across the floor in a clockwise from Zone 1 to Zone 4, other for duct installation which to allow for a start concurrent with other systems trades worked from Zone 4 to Zone 1. The pace for trades to complete a zone was three weeks, with trades following each other through the zones with a one-week separation.
By this time, it was understood that a permit issuance delay was a certainty, however the extent of the delay was unknown. Wise continued trade foremen lean construction training and coordination through the completion of enabling work, after which trades scaled back crews and focused on make ready work to ensure a rapid start once the permit was issued.
Planning to Overcome a 9-Week Permit Delay
After the permit was issued on October 12 John DaSilva, the project senior superintendent for Wise, met with the systems rough-in trades to modify the phase plan using a pull planning approach. Their goal was to release zones for in-wall rough-in inspections, with Zones 1 and 2 to be inspected by November 10.
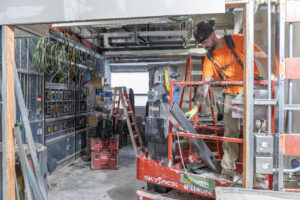
The clear workflow developed in the July 11 phase planning session allowed the team to develop and agree upon modifications to the plan while keeping the basic structure of the plan intact. Zones 3 and 4 were planned to be ready for inspection ten days later.
This ability to modify the initial clear workflow in the phase plan to rapidly ready spaces for in-wall inspections that release interior finish work was the first core contributor allowing Wise to overcome the delayed start.
On October 31 the Wise team met with the representatives from the interior finish trades, Newton-Wellesley Hospital, Colliers Project Leaders, and Perkins&Will to plan the interior finishes construction, using the strategic pull planning approach to develop the plan. With the experience gained through the adjustments to the systems rough-in plan Wise saw that they could plan this phase with smaller size zones, which were labeled blocks to not be confused with the systems rough-in zones.
In reviewing strategic options with trade foremen John established seven patient room blocks and three core area blocks on the floor. Each patient room block had four rooms, with 24 of the 28 rooms being patient rooms. Since the patient room blocks all had similar levels of effort by all the major trades working in those spaces the team pulled one typical block, and then replicated that workflow for the other six blocks.
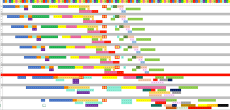
The core nursing support area in the middle of the floor had three distinct sub-areas, each requiring different levels of effort and combinations of trade operations. To address this variation in anticipated workflow between sub-areas, the core area was divided into three blocks, with the workflow sequencing and pacing planned separately. The plan anticipated trades moving into the core area blocks after completing the patient room blocks. The relatively small blocks allowed for a trade to complete an operation in each patient room block in two days, after which the following trade would begin work in that block.
The short duration between handoffs supported the team’s development of an interior finishes plan that would meet the original substantial completion date and was the second core contributor allowing Wise to overcome the delayed start.
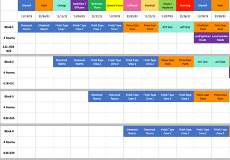
With the interior finishes planned for the on-time completion, on January 23, 2024, Wise led a planning session for the commissioning and startup work required before the space would be substantially complete. This work included controls and airflow balancing, medical panel testing, nurse call programming, hospital IT equipment installation, and final occupancy inspections. The collaborative planning in this session ensured that all commissioning work required for a successful completion was coordinated with the construction activities, avoiding conflicts that would lead to delays.
Executing the Plan
While the plan illustrated a path to an on-time completion, the team still needed to execute the plan. Two-day durations between trade handoffs facilitate quicker completions because they allow the latter phases to start work much earlier than do traditionally planned schedules. There is a tradeoff with this strategy, in that short durations between handoffs have a smaller time buffer for work pace variability. They also create a condition on midsized projects of more people onsite and more work in progress. These factors place greater demands on the quality of the daily management of the project team.
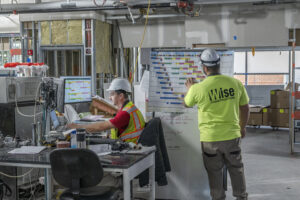
There were challenges to work progress during the implementation of the plan. Logistics related to floor finish installation required some adjustments to how work flowed around the floor. The clear plan developed in October, updated and posted onsite, allowed John to make adjustments that while not matching the plan in terms of block sequencing helped him work with trades to keep their work productively flowing.
The daily management of the workflow by the Wise team, necessary to address conditions in the field, was the third core contributor allowing Wise to overcome the delayed start.
Another challenge with rapid handoffs between trades is that coordination between builder and designer becomes more critical, as time to resolve field problems is minimal. To support the rapid handoffs and quicker pace of room completion project designers met with the Wise superintendents and trade contractor foremen twice weekly to review and agree upon how to address concerns. The result was a large reduction of risk for work delays, and a reduction in effort required to address formal requests for information.
This frequent onsite collaboration between design and construction professionals was the fourth core contributor allowing Wise to overcome the delayed start.
Summary
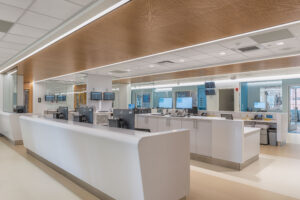
The original 10-month schedule for this healthcare project was considered aggressive, especially with less than 8 months available for the work requiring a building permit. Recognizing the challenge, the Wise project team began the implementation of lean construction practices before the team was aware of the circumstances leading to the permit issuance delay.
- By focusing on developing zone-based, balanced workflow the project team initially established a systems rough-in plan that would comfortably meet their original in-wall inspection milestones. Once the permit was issued, nearly nine weeks after initially planned, the project team was able to modify the rough-in plan to release the start of interior finish construction quickly.
- Short duration handoffs developed in the interior finishes planning session allowed the project team to chart a course to an on-time completion. In addition to pulling work sequences, it is important to balance trade crew capacity so that each trade operation completes work at a similar pace.
- When field conditions caused the work to vary from the interior finishes phase, daily management practices allowed the team to us the structure of the plan to make adjustments that kept work flowing so that time was not lost.
- Short duration handoffs surface design questions that require quick resolution by the project team. Twice weekly onsite collaboration between design and construction professionals greatly reduced the risk of a design coordination issue slowing construction progress.
The approach requires a different mindset than traditional project scheduling, which establishes a “best” way forward by treating project schedules as a sequential connection of individual parts. Instead, the planning and execution approach implemented by Wise treated the project schedule as workflows that must be managed as a unified system, ideally with the support of design professionals and project owners and their representatives, as was the case with this project.
That is why the Wise project team, with the support of Newton-Wellesley Hospital, Colliers Project Leaders, Keel Project Management, Perkins&Will, BR+A Consulting Engineers, and RisingTerrain, was able to overcome a more than 25% delay to the start of their work and still finish on time.
Brenden Lydon is a Senior Project Manager at Wise Construction.
John DaSilva is a Senior Superintendent at Wise Construction.
Tom Richert is a Principal at RisingTerrain LLC.
Other key Wise Construction project team members.
Brian Vatelle, Project Manager
Justin Davis, Superintendent
Marty Leik, Corporate Safety Director
Eric Raposo, Carpenter Foreman
Paul Menini, Labor Foreman
About Wise Construction
Wise Construction provides preconstruction, construction management, virtual design & construction, MEP services, design-build, and self-performance services, specializing in occupied space renovation and building conversion projects. Wise works with science & technology, healthcare, and institutional clients throughout the Greater Boston area. The success of the firm has been bolstered by the local knowledge and relationships it has earned through more than four decades of service to its clients.
WiseConstruction.com
About RisingTerrain
RisingTerrain LLC is a project performance consultancy equipping project teams with the executive skills required to lead and rapidly deliver quality projects at reduced costs. RisingTerrain serves clients throughout the U.S., supporting healthcare, technology, manufacturing, institutional, multifamily, and government projects. The firm continually builds its capabilities, through the introduction of leading organizational performance practices to client project leaders.
RisingTerrain.com