W. Edwards Deming, an influential business theorist, statistician, and management consultant, significantly influenced quality management practices. His work played a role in the evolution of the Toyota Production System and the business practices of many other companies in Japan, and ultimately in the USA. Deming’s ideas helped Toyota focus on reducing variability and improving processes, aligned with its culture of continuous improvement. His contributions are widely recognized as foundational to lean practices.
One notable practice that Toyota pioneered is target costing. This cost management strategy involves setting cost targets during the design phase and striving to meet these targets through design and production efficiencies. Target costing enabled Toyota to maintain cost control while delivering high-quality products, a practice that other manufacturers have since adopted. The principle is that the market sets the price for a product, and production costs must be equal to or less than this price minus a target profit.
Target Value Design adapts target costing to the architecture-engineering-construction (AEC) industry. This adaptation is necessary due to the multiple stakeholders involved in building design, which adds complexity to coordination. However, the core principle remains achieving a cost that the market supports while ensuring profitability for stakeholders.
Early Engagement of Project Stakeholders
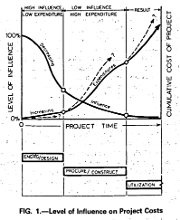
Target Value Design and the later development of Target Value Delivery (TVD)[1] emphasizes the early integration of construction expertise with design expertise, supported by project owner involvement in decision-making. Decisions are informed by program and aesthetic requirements along with costs, aiming to achieve project goals at or below a target cost. Early construction expertise reduces costs by recommending design solutions that minimize construction complexity without compromising quality. Continuous cost modeling prevents investment in developing solutions that cannot meet cost targets.
The concept of early involvement in building design by construction professionals predates TVD. The MacLeamy Curve, a rough contemporary to TVD was introduced by Patrick MacLeamy in 2004. A similar curve, shown on the right, was proposed by Boyd Paulson in 1976.[2] These curves highlight the importance of front-loading design efforts, as changes become more difficult and costly later in the process.
Back to Deming – Applying His Approach to TVD
In The New Economics, Deming advocates for front-loading effort and product development time in the earliest stages.[3] He recommends that each subsequent stage require less effort than the previous one. There is a focus on reducing rework due to design deficiencies and addressing design problems early ensures they are resolved when least costly.
I propose testing a structure with greater initial design effort than most TVD approaches, encouraging early design effort by a full project team.[4] The proposed seven design stages, preceded by Business Case Planning and Validation, are:
-
-
- Set-Based Design Option Development and Convergence
- Option Investigation and Integration Tests
- Building Program Layout
- Production Design
- Detailed Engineering
- Finish Selections
- Shop Drawings and Product Submittals
-
Business Case Planning involves an initial assessment of the cost and value of a proposed capital asset, including project program description, parametric cost estimating, and modeling economic and other benefits. Investing about 0.1% of the anticipated project cost in Business Case Planning is recommended.
Validation tests the Business Case assumptions and findings, assessing whether design solutions meet the initial Conditions of Satisfaction.[5] If Validation fails, the project is halted. Investing about 1% of the anticipated project cost in Validation is recommended.
The first two stages constitute the Conceptual Design effort, requiring full engagement of engineering and construction professionals from the beginning. This allows for a full exploration of design options, increasing the probability of developing a high-value solution at a low cost. These stages are sequential.
The next four stages are the Detail and Production Design effort, including building design articulation, engineered components, and the strategic plan for project delivery. There may be some overlap between these stages. The seventh stage, often considered part of the construction phase, involves shop drawing and submittal confirmations, which are more appropriately part of the design process.
Below are the seven stages with recommended levels of effort for each stage expressed as a percentage of design effort costs. Using Deming’s guidelines, this distribution is subject to testing:[6]
-
-
- Set-Based Design Option Development and Convergence (21%)
- Option Investigation and Integration Tests (18%)
- Building Program Layout (16%)
- Production Design (14%)
- Detailed Engineering (12%)
- Finish Selections (10%)
- Shop Drawings and Product Submittals (9%)
-
Projects may benefit from compressing the time required for design stages rather than overlapping construction and design, which can lead to rework. Each stage represents continuous workstreams that can be sequenced using phase pull planning. The last five stages may have some degree of overlap, with colocation facilitating shared work and collaborative problem-solving.
Set-Based Design Option Development and Convergence (21%)
Set-Based Design examines possible combinations of major building elements. The project team expands the number of possible design solutions, then converges on three or four most promising designs. This stage requires significant effort to develop feasible subsystem solutions and understand their costs.[7]
Option Investigation and Integration Tests (18%)
The project team organizes into cross-disciplinary work clusters to assess the most advantageous design solution. Continuous cost estimating informs each cluster of the financial impact of design decisions. Integration events test the cohesiveness of design solutions. At the end of this stage the project team has a design solution with all building systems fully integrated.
Building Program Layout (16%)
This stage focuses on developing architectural design elements, with engineering cluster members supporting the architectural clusters. Design issues include space layout, envelope design, and equipment selection. Long lead equipment items may be determined and ordered during this stage.
Production Design (14%)
The construction planning cluster organizes construction elements into workstream modules, developing strategies for constructing each module. Prefabrication elements, material logistics, and site safety planning are addressed.
Detailed Engineering (12%)
Systems engineers detail the placement of equipment and distribution of utilities. Organizing design workflow to begin detailed engineering after layout completion eliminates rework.
Finish Selections (10%)
Final specification of finishes occurs in this stage, with mockups used to confirm selections.
Shop Drawings and Product Submittals (9%)
Preparation of shop drawings and product submittals is integrated into this final construction documentation stage, providing a fully vetted set of building instructions.
Conclusion
The integration of Deming’s principles into TVD offers a robust framework for enhancing quality and efficiency in architectural design and construction. By front-loading design efforts and involving all stakeholders early in the process, we can significantly reduce rework and optimize project outcomes. The proposed seven-stage design process ensures a comprehensive and collaborative approach to project delivery.
This methodology aligns with Deming’s emphasis on early problem-solving and adapts to the unique complexities of the AEC industry. By leveraging Set-Based Design and continuous cost modeling, project teams can develop high-value solutions that meet cost targets and client expectations. The structured involvement of construction professionals throughout the design stages enhances the feasibility and constructability of the design, leading to higher quality and more predictable project outcomes.
In conclusion, applying Deming’s product design approach to TVD represents a significant advancement in our pursuit of excellence in design and construction. It encourages a culture of continuous improvement, collaboration, and innovation, ensuring that we deliver projects that are not only cost-effective but also of the highest quality.
RisingTerrain LLC is a leading capital project performance consultancy. Clients learn practices capable of delivering projects 10-20% faster while strengthening systems for future initiatives. Our clients span healthcare, technology, manufacturing, pharmaceutical, and government sectors.
We enhance project team performance by equipping them with the skills to lead and deliver quality projects efficiently. Our methodologies focus on internal coaching and developing subject matter expertise within client organizations.
RisingTerrain.com
Notes
[1] The initialism TVD is used to refer to either Target Value Design or Target Value Delivery. The terms are not strictly interchangeable as the latter extends the concepts of the former across the entire span of the project delivery process. This distinction is not relevant to the points discussed in this article.
[2] The MacLeamy Curve conveys a concept not entirely new when Patrick MacLeamy developed this concept in 2004. The Linbeck Group based in Houston provided client with a similar curve in the 1990s to argue for the importance of builder expertise during design. Boyd Paulson’s paper, “Designing to Reduce Construction Costs,” published in December 1976 by the American Society of Civil Engineers (ASCE) Journal of the Construction Division, Volume 102, Issue 4, was presented at the April 1976 ASCE National Water Resources and Ocean Engineering Convention in San Diego. A main conclusion of Paulson’s paper is that suboptimization of project costs through competitive bidding of professional services is “likely to produce much higher costs in the long run.” (https://doi.org/10.1061/JCCEAZ.0000639)
[3] The New Economics was first published in 1994. In the text Deming provides a recommendation for reducing the time for product development by putting more effort into the early stages so that each stage receives more effort than the following stage. His recommendation is that the effort, in terms of cost, of any stage be 1 – x times the level of effort of the preceding stage. It is necessary that x is some number less than 1 for there to be any effort in the following stage. For illustration purposes only Deming published an example in which x was equal to 0.2. In his illustration this leads to the level of effort in the 9th stage of a development process to be 43.3% the level of effort of the initial stage.
[4] While Target Value Delivery is a well-defined methodology, the application and effectiveness of the methodology varies among project teams. One of the motivations for this article is to encourage and give support to project leaders who advocate for early design effort by a full project team.
[5] Conditions of Satisfaction articulate the promises that must be met for work to be considered successful. All Conditions of Satisfaction promises are time bound. The Conditions of Satisfaction developed for the Business Case are not to be confused with the project team Conditions of Satisfaction, which can only be developed after a team has been enrolled onto the project.
[6] Using Deming’s product development stage investment guidelines, I reviewed a range of distributions for x equaling 0.1 to 0.2 and settled on x equaling 0.14, rounding the percentages to whole numbers. This is my initial sense of an appropriate distribution. Because design costs as a percent of project cost varies by building type and other factors, I am expressing design investment recommendations as a percent of overall design costs regardless of construction costs. The overall design effort should be tailored to the needs of the project.
[7] I sense this investment of effort into a Set-Based Design practice is the largest departure from how TVD is usually practiced. Conventional building design practice ignores this step altogether. Not including a robust Set-Base Design effort leaves potentially great design solutions undiscovered. This stage is also an important step toward identifying well integrated building systems for further design development.